The Green Building Council of Australia’s (GBCA) Green Star program is an internationally recognised rating system that delivers independent verification of sustainable outcomes throughout the life cycle of the built environment.
Since Green Star introduced the life cycle assessment (LCA) credit as an innovation challenge for the building industry in 2014, it has been relatively easy for projects to earn most credit points available by having good operational energy performance. This makes sense – after all, over 60 years, operational energy stands out as the most impactful life cycle stage for most environmental categories.
However, the parameters of the LCA credit largely missed the point, which was to drive improvements in the area of materials. Additionally, not only did good energy performance give a good LCA credit score, it was also awarded in the Greenhouse Gas Emissions credit, hence projects with good energy performance could double dip to earn easy points.
The GBCA recently released v1.2 of the Interiors and Design & As Built Green Star rating tool, with several noteworthy updates and improvements. Of significance and special interest to Edge Impact are the changes to the Materials and Life Cycle Assessment credit – 19A specifically.
In v1.2, there is increased emphasis on how the LCA has been applied to reduce the environmental impact through material selection, construction process improvements or direct influence into the design review process, and incentives to drive its continual application.
Actioning the value and insights made available from LCA
In Green Star v1.2, LCA points from operational energy reductions are capped. Previously, projects could gain full points through good operational energy performance and going the extra mile on reporting of impacts, but now these factors earn a maximum of 3/7 for Design & As Built and 12/19 points for Interiors.
To get the full score, projects also need to demonstrate outcomes and the use of LCA in decision-making through:
- LCA design review: This includes considering LCA-based impacts in conceptual design discussions. This can include the first iteration of the LCA results being presented to the building’s design team early enough to influence design decisions. For Green Star rating purposes, this process and the outcomes need to be documented and described.
- Material selection improvement: The LCA must be used to drive material selection improvement. For example, the project team can use the first iteration of the project LCA to identify hotpots and opportunities to reduce impacts from materials through strategic sourcing (selecting a supplier with a lower impact product), design for dematerialisation, or substituting a high impact material for a lower impact alternative (think timber versus steel frame).
- Construction process improvement: This aspect focuses on finding environmental and resource savings in the transportation of materials and products to site, and from direct construction impacts. This could, for example, include local sourcing, which reduces the need for long distance transport of materials. It could also include energy and resource efficiency in construction.
Points are still available for reporting on additional life cycle impacts (low hanging fruit from a Green Star credit perspective, as very little effort is required to meet this requirement).
Tips: In terms of tips and tricks, not a lot of people are aware that using products with Environmental Product Declarations (EPDs) is a very simple and effective way to demonstrate material selection improvements – selecting a lower impact product over a higher impact product. It’s also an opportunity to double dip and earn Sustainable Products credits (credit 21C). In fact, most Australian-made steel, timber and plastic pipes carry EPDs already, as well as several mainstream building products from James Hardie, Dulux, InnoWood, Kingspan, etc.
Questions left unanswered and what the next version may look like
Although the above focus makes a lot of sense to drive improvements in building materials, it leaves a few questions unanswered. For one, Green Star still assumes technology and the electricity grid mix stays the same, which probably isn’t completely realistic. With the focus on de-carbonisation towards zero carbon buildings and clean tech in general, chances are the buildings of the future will have a much lighter footprint in operations than we see today.
Trade-offs between embodied and operational impacts have not been solved conclusively. For example, investing in more materials (double glazing, insulation materials) to achieve better net outcomes from improved energy performance, something LCA typically deals with well, is stifled a bit with the introduced point cap for operational improvements.
Green Star’s LCA ‘holy grail’ probably needs a radical shake-up and bold steps forward, including:
- Let’s group materials, waste, water, greenhouse gas emissions and energy, and other emissions into a super LCA credit. Let’s optimise the whole building across all relevant environmental dimensions and life cycle stages, just like the founding LCA fathers intended back in the 70s.
- Let’s embrace the changing world. Let’s optimise the buildings with a view that technology, consumption and production patterns, and energy systems are changing and evolving. We should factor in the future of the built environment when we design to ensure the buildings we create will be relevant in the decades ahead.
What else has changed in v1.2?
A few more changes to the credit worth mentioning:
- Additional pathway to demonstrate LCA expertise: Green Star recognises a person who is qualified as an ‘LCA Certified Practitioner’ through the Australian, NZ or US life cycle assessment societies.
- More independence requirements for the peer review: Previously it was possible to conduct the required peer review of the LCA internally, if the reviewer was not part of the project team. This has changed – now the LCA practitioner and peer reviewer cannot be the same individual or from the same organisation.
Edge Impact has a wealth of experience in risk assessment and life cycle assessment. To find out more about how we can help your organisation, please contact Scotty Matyus-Flynn (scott.mf@edgeimpact.global).
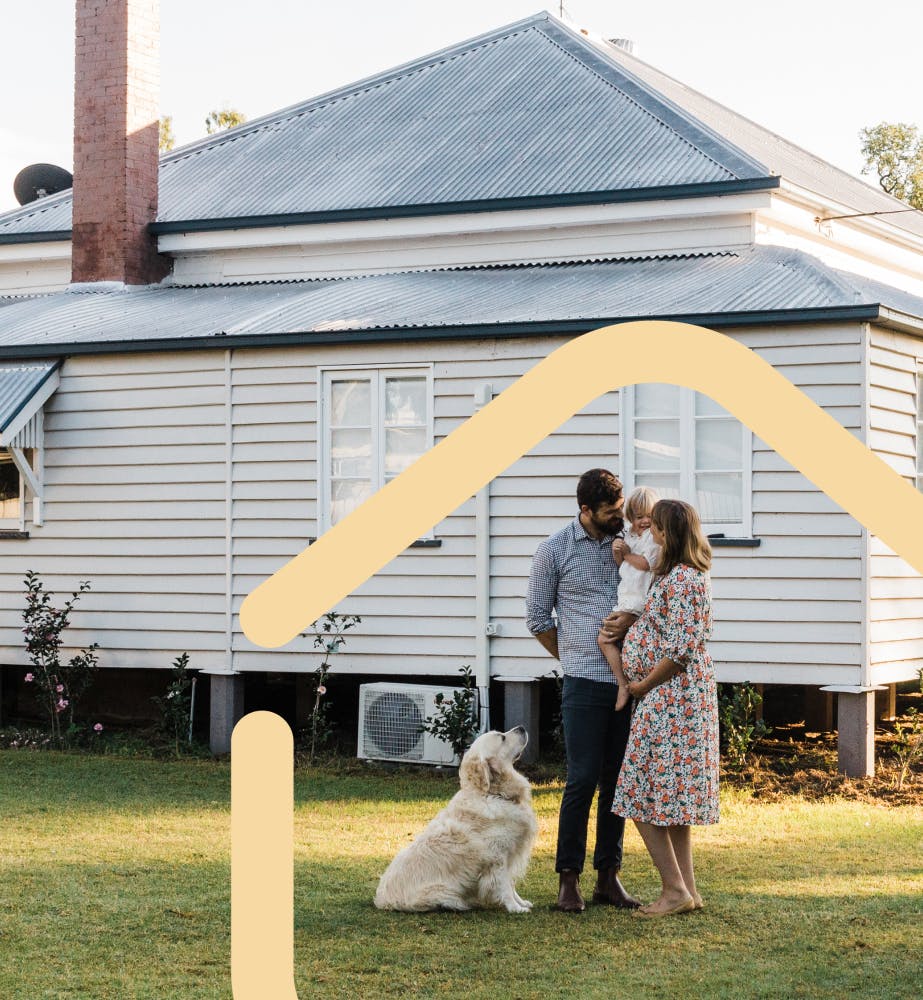
CRJO partnered with Edge to develop a toolkit for retrofitting homes, boosting bushfire resilience for homeowners, councils, and industry.